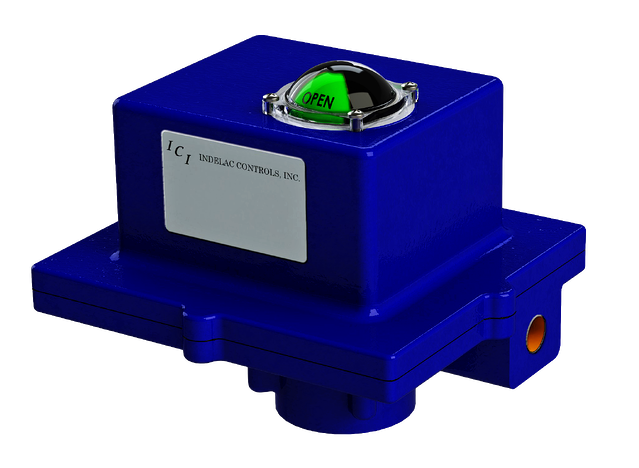
Powder Coating Steps
- Sandblast the product after fabrication.
- Start applying the powder.
- Once the powder is applied it is moved from the powder coating bay into the oven where it is heated up to gel the primer.
- Once the primer becomes heated and gelled it is moved back into the powder coating booth where the finished coat is applied.
- Finally, the product is baked in the oven until it is fully ready to move to the next stage of manufacturing.
What are the benefits?
- Powder coating materials contain no solvents.
- Powder coating materials require no venting or filtering.
- Powder coating saves energy and cuts cost.
- It is difficult to make powder coating run, sag, or drip, so it has a presentable appearance on products.
- Operators who apply powder coating require minimal supervision and operator training.
- Products of powder coating are able to resist corrosion and prolong the life of the product.
What does Indelac use?
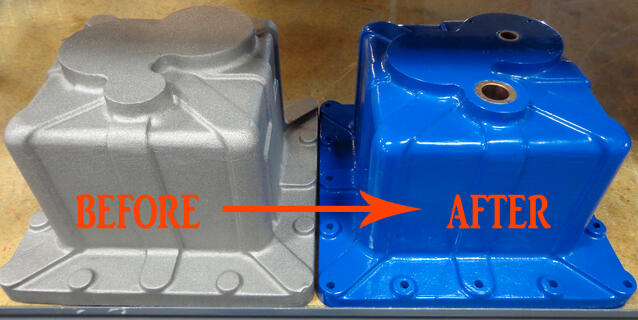
Technical Data of Indelac Blue
TYPICAL PROPERTIES |
TEST METHOD |
RESULTS |
Specific Gravity |
PCI #4 |
1.55 |
Coverage |
Theoretical |
125 sq. ft./lb. @ 1 mil |
Gloss at 60˚F |
ASTM D523 |
80+ |
Pencil Hardness |
ASTM D3363 |
2H |
Direct Impact |
ASTM D2794 |
Min 100 in. lbs. |
MEK Resistance |
PCI #8 |
50 Double Rubs |
APPLICATION |
CURE |
FILM THICKNESS |
Electrostatic Spray |
10 minutes at 400˚F |
2.0-3.0 mils |
*Technical Data provided by Alpha Coating Technologies, LLC.
Using this system delivers confidence in our products. Protecting our actuators is something we take pride in. Reliable and safe field device operation is a crucial industry component. Electric actuators are used to automate industrial valves of any type and size. Since these and other actuators are used wherever pipework or even industrial valve automation are needed it is crucial that these actuators are safe from any possible corrosion. Even in water treatment plants, sewage treatment plants, refineries, or oil drilling rigs it is important to be sure that the products will not corrode and that their appearance will last through wear and tear.
Corrosion occurs, but not with Indelac Powder Coated Actuators.
There has been a continuous development in the world of exploration engineering. This in fact has implemented soaring energy cost that allow for the intensification of oil and gas extraction and various environmental conditions including the open sea, tropics, and polar latitudes. Since these environments are often salty, wet, humid, sandy, and have various air flow it is important to be sure the conditions do not put a toll on the actuators and other products. In the past few years many operating companies and other companies have become more aware of corrosion protection issues, Indelac Controls included. There are many corrosion categories one must be aware of.
Corrosive Category |
Examples and Explanation |
C1- Very Low |
Indoor Only. Includes heated buildings with clean atmospheres. |
C2- Low |
This includes rural areas and unheated buildings where a chance of condensation is possible. This includes sports halls, depots and warehouses without climate control. |
C3- Medium |
This includes Urban and Industrial atmospheres that have a moderate air pollution as well as coastal areas with a low salinity. This includes rooms with a high humidity and some possible air pollution. Examples are breweries and food-processing plants. |
C4- High |
This includes Industrial areas as well as coastal areas with moderate salinity like some chemical plants. |
C5-I- Very High (Industrial) |
This includes industrial areas with high humidity and an aggressive atmosphere. |
C5-M- Very High (Marine) |
This includes coastal and offshore areas with high salinity as well as buildings in areas with almost permanent condensation and with high pollution. |
Conclusion
Under certain circumstances, it is possible that corrosion will appear at corrosion resistant component joints if there are is presence of combined materials. It is important to know that currently there is no known comparably effective corrosion protection available in the actuator market. This is also not something that happens in a day, these techniques take time to develop. Indelac Controls is committed to the overall appearance of our products and assures that our powder coating system is top of the line.