Understanding the differences between regulators and control valves is crucial in the automation industry. Each of these holds equal importance but have different functions and also operate in a different way. It is important to be knowledgeable about both solutions so that control process designers do not engage in major problems or waste money and resources.
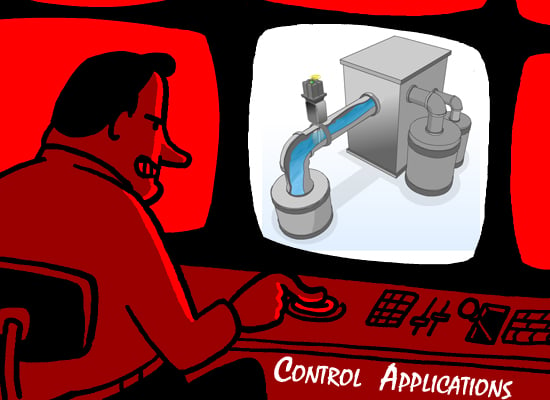
Understanding the Difference
First, in order to understand the differences between regulators and control valves we should look into the components of each. In terms of design, a typical control loop allows control valves to employ a range of process variables. This depends on which variable is being measured for control (flow, level, temperature, pressure…). The process control variable is first measured by a sensor or transmitter and then sent to a host control system. More times than not, this system is known as the DCS or Distributed Control System. This system is responsible for interpreting how the valve should respond to a deviation from the set point value (predetermined). After this occurs a signal is communicated back to the DCS control which in return reports the degree of which the actuator needs to close or open the valve in order to return back to the predetermined set point.
Operationally, the main difference between a control valve and a regulator is that regulators are better defined as process powered valves without the demand for an external power or even an instrument air source to operate. Typically, a regulator applies the pressure of the controlled process fluid against a diaphragm. The same diaphragm then rejects a compressed spring in order to achieve forced balance with the diaphragm at a given set pressure. If there is any change in the controlled pressure the diaphragm is forced to move. This then causes the flow area of the regulator to change which allows more or less process fluid to flow.
Since the use of process fluid pressure is a means for control, regulators are functional as pressure control valves.
Another difference comes in relation to the design pressure rating of the body of the regulator. Control valves are able to handle the same pressures on the outside of a valve as they are on the inlet side. However, a regulator may have a lower pressure rating on the control pressure side of itself (the regulator). Why? You might ask. This is because the process fluid pressure is being directly applied to the components of the diaphragm casing.
One more difference is speed. Compared to control valves, a regulators speed of response is faster. Regulators are able to respond instantly to changes occurring in the controlled pressure.
As far as maintenance they are also easier to maintain and have no volatile emissions.
Control valves, however, are available in larger sizes and are in higher pressure classes than regulators are.
Choosing the Right Solution for the Right Application
Regulators, usually, are associated with a lower cost for maintenance and installation. But it is also important to keep in mind that many projects spec in the use of an actuator with its valve for their control applications.
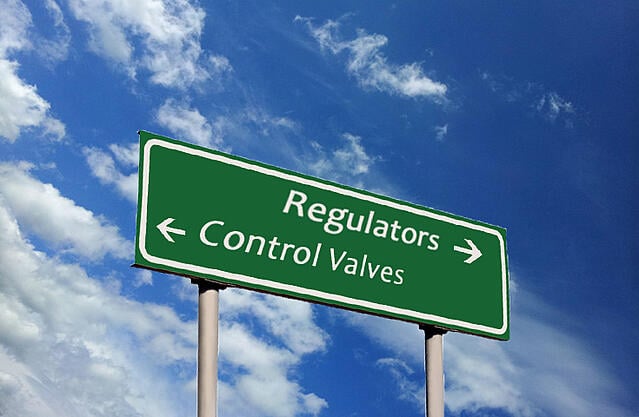
In some situations a control actuator and valve package or a regulator should not be used. This is due to the fact that certain applications mean technical advantages for either a control valve or a regulator. Some of these examples include:
- Tank Blanketing
- Differential Pressure Control
- Boiler and Heater Control
- Extreme Service Conditions
Knowledge-based decision
Understanding the differences between regulators and control valves is crucial in the automation industry. Each of these holds equal importance but are different in the way they function and operate. If one understands the capabilities and functions of valve actuators as well as regulators, those whom are tasked to select from the two options will be able to select with confidence.